Our new NorthStandard site is now live. There will be no new content or updates added to this site. For the latest information, please visit our new site north-standard.com.
Decarbonisation in shipping: Options to achieve compliance
News & Insights 11 November 2021
As per a recent scientific report, human activity is changing the climate in unprecedented and sometimes irreversible ways - weather patterns are changing, sea levels are rising, and extreme weather events are becoming more...
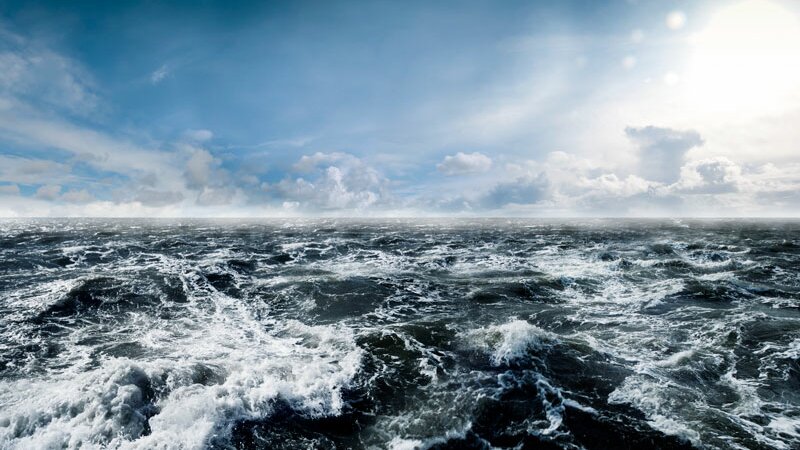
As per a recent scientific report, human activity is changing the climate in unprecedented and sometimes irreversible ways - weather patterns are changing, sea levels are rising, and extreme weather events are becoming more frequent and ferocious. The United Nations (UN) has described the findings of this report as ‘code red’ for humanity.
As a specialized agency of the UN, the International Maritime Organization (IMO) has committed to contribute its efforts to combat climate change and its impacts.
During the seventy-sixth session of the IMO’s Marine Environment Protection Committee (MEPC-76), held in June-2021, a great proportion of time was devoted to delivering mandatory goal-based technical and operational measures for the reduction of greenhouse gas (GHG) emissions. These amendments will enter into force on 1 November 2022 and applied from 1 January 2023.
This goal-based approach allows shipowners and operators to achieve the annual carbon intensity reduction factor through a combination of following technical and operational measures:
- calculation and verification of Energy Efficiency Existing Ship Index (EEXI);
- introduction of a rating mechanism (A to E) linked to the operational Carbon Intensity Indicator (CII); and
- enhanced use and auditing of Ship Energy Efficiency Management Plan (SEEMP).
Decarbonisation solutions for vessels
As highlighted in the club’s previous article, the energy efficiency design index (EEDI) requirements for new ships(1) have been in force for a while.
From 1 November 2022, existing ships will have to calculate the attained Energy Efficiency Existing Ship Index (EEXI) and determine if it is equal to or lower than the required EEXI; while the EEDI-certified ship will have to determine whether the attained EEDI is equal to or lower than the required EEXI.
Ships that have an attained EEXI/EEDI less than or equal to the required EEXI, will have to prepare the EEXI Technical file (which includes the data used for calculation of the attained EEXI) and apply to Flag Administration for the issuance of the International Energy Efficiency Certificate (IEEC). However, in cases where the attained EEXI/EEDI is greater than the required EEXI, there will be a need to take action to improve the attained EEXI.
In addition to retrofitting of energy efficient technologies (EETs) or switching to a lower carbon / carbon neutral fuel, the EEXI regulation allows the use of overridable power limitation – including both engine power limitation (EPL) and shaft power limitation (SHaPoLi) – to limit operational engine loads and fuel consumption. This solution is relatively non-invasive, has a low capital cost, and is applicable to most ship types. However, its ability to impact subsequent CII ratings will be limited.
A study done in 2020 by the International Council on Clean Transportation (ICCT) mentions that “EPL scenarios below 30% provide negligible cuts in CO2 for the 2018 fleet, while a 30% EPL is estimated to reduce CO2 by 2% for container ships and oil tankers, and 3% for bulk carriers. Larger, 50%+ EPL could more meaningfully reduce ship CO2 by 8%–19% depending on ship type and size. Additionally, and importantly, benefits diminish over time if EPL is not required for newer ships due to fleet turnover and growth.”
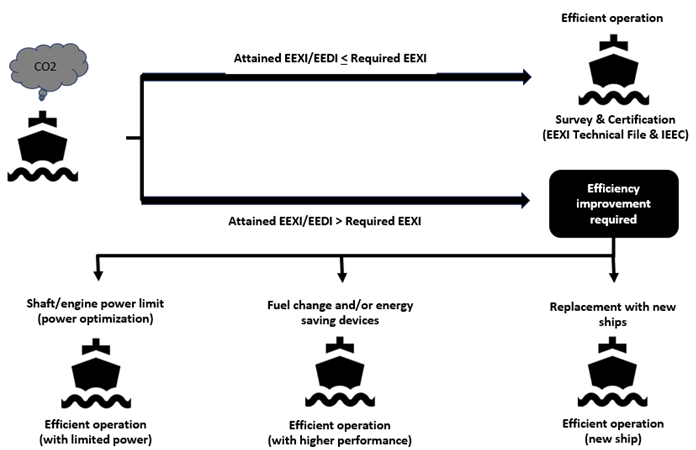
Additionally, members will need to consider steps to address operational carbon intensity reduction simultaneously. As CII is based on how a ship is operated, its value can be improved by:
- operating at a reduced speed or slow steaming;
- weather routing;
- reducing cargo intake;
- improving general condition of the ship (i.e., hull cleaning & coating);
- switching to a low-carbon or carbon neutral fuel;
- installing energy efficient technology, like hull air lubrication systems, wind assistance, etc.
Comparison of alternative fuels and emerging technologies
In terms of the alternative fuels and emerging technologies, there is no one-size-fits-all solution, and a lot of considerations will go into selecting appropriate option based on ship type/age, trading area, retrofitting costs, operating budget, fuel price/availability, infrastructure development, safety issues, etc.
LNG, LPG, biofuel, methanol, ammonia, and hydrogen, as well as the usage of fuel cells and batteries, are some of the main options. Each has its own set of advantages and disadvantages and switching between them is not easy - engines and other machinery will need to be capable of burning the fuel in question.
There are numerous other considerations in relation to the various fuel options. For example, biofuel brings a handful of technical challenges such as oxidation stability, cold flow properties, risk of microbial growth, clogging of filters, and increased engine deposits; and hence, it requires careful handling.
Handling of other alternative fuel options on vessels could be complex as well and will require a highly trained crew. Most of the gases in liquid form requires storage at cryogenic temperature - specific safety standards will need to be satisfied. Hydrogen, for example, has a wide flammability range, while ammonia is highly toxic. Stringent measures will be required to protect crew from exposure.
Hydrogen is a clean fuel; however, manufacturing hydrogen fuel is energy-intensive and has carbon by-products. What is now called brown hydrogen is created through coal gasification. The process for producing grey hydrogen from natural gas throws off carbon waste. Blue hydrogen uses carbon capture and storage for the greenhouse gases produced in the creation of grey hydrogen. Green hydrogen production – the ultimate clean hydrogen resource – uses renewable energy to create hydrogen fuel, which could be quite expensive.
Similarly, green ammonia will cost two to four times as much to make as conventional ammonia. The green and blue ammonia value chains differ in the hydrogen production method used; green ammonia being generated from water electrolysis and blue ammonia being generated from a conventional pathway, using natural gas, but with the addition of carbon capture.
In terms of storage capacity, energy density/calorific value of the fuel is critical. More storage space on the ship will be required if a fuel does not have an energy density that is at least comparable to what it has now. Hydrogen, ammonia, and methanol, for example, have a lower density, requiring larger tanks onboard ships.
For a fuel to become widely used, it must have adequate scalability, i.e., both the infrastructure and the demand must be there. This may be easier for ships on regular liner route, but ships traveling between ports will have a difficult time finding the relatively scarce option.
Most of the alternative fuels and technologies are still undergoing technical, economic, and environmental review. However, in order to evaluate the commercial and operational viability of alternative fuels, we have listed below some of the pros and cons of the options available.
Alternative fuels | Advantages | Disadvantages |
Liquified Natural Gas (LNG) |
|
|
Liquified Petroleum Gas (LPG) |
|
|
Biofuels |
|
|
Hydrogen (H2) |
|
|
Ammonia (NH3) |
|
|
Methanol (CH3OH) |
|
|
Energy efficiency technologies (EETs) | |
Hull form optimisation | Hull optimisation focuses on minimising the wave resistance and friction between water and hull. The reduced frictional resistance increases energy efficiency of the ship, particularly at reduced speeds. Following are the ways by which hull hydrodynamic performance can be improved:
Optimisation measures are generally applied on new-built ships but also applicable to retrofitting of existing ships. However, it is important to understand in detail the ship’s performance and its operating profile before considering any design modification. Usually, a comprehensive series of model tests and computational fluid dynamic (CFD) assessments are required in such cases. When considering hull form optimization, it is beneficial to include sister ships in the CFD analysis to reduce the cost for the fleet. |
Hull coatings | One way of lowering the frictional resistance is to improve the smoothness of a hull by means of coatings that reduce fouling. In recent years there has been a lot of development in the coating technology, e.g. introduction of hydrogel, a component that traps a microscopic layer of water on the coating’s surface, smoothing the water flow around the hull. The use of hydrogel containing coatings makes the surface of the hull behave like a liquid on a microscopic level. This not only deters the fouling from settling in the first place, but also significantly reduces hull friction. |
Air lubrication | Air lubrication is a method to reduce the frictional resistance between the ship’s hull and water using a sheet of air or air bubbles. This reduction creates energy-saving effect and cuts down on the fuel consumption of the ship. An automation system regulates the compressors/blowers depending on speed. In ideal situations, an air injection system can achieve up to 15% in the reduction of CO2 emissions together with significant fuel savings. As compared to ships with V-shaped bottoms, this system is more effective on flat bottoms as because the air on a V-shaped bottom will flow away much more easily than a flat bottom. |
Propellers and Rudders | Numerous devices have been designed for improving the ship’s energy efficiency by recovering as much as possible of the rotational energy in the flow from the propeller, or to provide some pre-or post-rotation of the in-flow into and after the propeller to ensure best performance. |
Electric (battery powered) propulsion | In recent years, pure battery-electric propulsion, using Lithium Ion (Li-ion) batteries, has been successfully applied on small, short-sea vessels. The potential for batteries in combination with a two-stroke main engine in a hybrid system is being evaluated for larger ocean-going vessels. |
Hydrogen fuel cells | Hydrogen fuel cells works in a similar manner to an electric battery, i.e., it converts chemical energy into electrical energy using the movement of charged hydrogen ions across an electrolyte membrane to generate current. There they recombine with oxygen to produce water – a fuel cell’s only emission, alongside hot air. It does not deplete or need charging and has a higher power density and lower weight than batteries. However, it is expensive and any leakage, if not handled properly, may cause hydrogen accumulation and explosion. Therefore, the hydrogen storage place and fuel cell cabin require appropriate measures to ensure safe integrity levels. |
Shore to ship power (cold ironing) | This is the process of providing shoreside electrical power to a ship at berth while its main and auxiliary engines are turned off. When a ship is in port, auxiliary engines (generators) are commonly used to provide required power for cargo operations, emergency equipment, cooling, heating, lighting as well as domestic use. By simply turning off generators and plugging in to an electrical supply point in the ports, fuel consumption saving and subsequently reduction of noise and air emission can be achieved. Smaller vessels with low power requirements can make use of normal grid voltage and frequency. However, for larger vessels with high power requirements only limited ports may be able to provide this facility. |
Waste heat recovery systems | A waste-heat recovery system (WHRS) recovers the thermal energy from the exhaust gas and convert it into electrical energy, while the residual heat can further be used for ship services (such as hot water and steam). The system can consist of an exhaust gas boiler (or combined with oil fired boiler), a power turbine and/or a steam turbine with alternator. Redesigning the ship layout can efficiently accommodate the boilers on the ship to better fit these systems. There is a potential for a reduction in main engine fuel consumption estimated at 3% to 8% which contributes to emissions reductions overall. Waste heat recovery is well proven onboard ships, but the potential can be variable depending on the size, numbers, usage and efficiency of the engines on board. Furthermore, these measures are usually not relevant for retrofitting, due to large costs and efforts related to redesign, steel work, extra weight, etc. |
Carbon capture and storage | This technology is at very early development stages for ships. It involves isolation and capturing carbon emissions from the ship’s exhaust and preventing them from entering the atmosphere. However suitable cryogenic storage tanks are needed to collect liquid cargo until the ship reaches port. Thereafter, the carbon can either be stored permanently under the ground in geological formations or utilised in carbon-consuming industries. |
Solar panels | Solar panels are devices that convert light from the sun into electricity. Solar panels on ships are not very common at present, but some installations have been done over the last years on certain types of ships including car carriers, bulkers, passenger ferries and smaller domestic vessels by using marine grade solar panels. This solution may not suit container vessels because of the space required. This technology is in its infancy and is expected to become less expensive over time, but the panels are unlikely to become much more efficient or less space consuming. |
Wind assisted propulsion systems | Wind-assisted propulsion systems (e.g., sail, kite, fixed-wing, Flettner rotors) utilises an old concept with a modern edge. The IMO has recognized this technology and included the effects of wind propulsion in MEPC.1/Circ. 815. However, it is considered as an auxiliary propulsion system that augments the primary propulsion system. In fact, most wind-assisted propulsion systems require a secondary source of energy to be operated, e.g. Flettner rotors need to be started up by motors to develop their aerodynamic thrust forces. For such systems, the availability of wind and therefore the operation area of wind-assisted vessels is the most relevant factor. It is vital to consider operational costs (maintenance, spare parts, replacement of components, etc.) in addition to the fuel saving potential. |
Conclusion
The route to decarbonization involves consideration regarding fuel options, technology advancements and operational improvements. It is necessary to understand which option has the potential to deliver safe, scalable, and commercially viable solution. Considering all available options, and their suitability for specific vessels and operations, is key to ensuring a safer shipping industry as we move towards industry‑wide decarbonisation.
While it may be tempting to assume the timescale of any change is long, this would be a mistake. The way ships are operated and fuelled is already changing. Given the scale of upcoming challenges, evolving market conditions and regulatory landscape, it is imperative to start giving these issues a careful thought now.
Regardless of which option is chosen, alternative fuels will play a key role in the ultimate goal of achieving emissions reduction. Determining which of the fuel options is best suited can prove challenging. Understanding this predicament, the club has formed a working group and advisory panel that looks at many aspects around decarbonisation in shipping. This is aimed to assist members to prepare for the upcoming regulations and meet these challenges.
(1)As per IMO RESOLUTION MEPC.203(62), 'new ship' means a ship:
for which the building contract is placed on or after 1 January 2013; or
in the absence of a building contract, the keel of which is laid or which is at a similar stage of construction on or after 1 July 2013; or
the delivery of which is on or after 1 July 2015.