Our new NorthStandard site is now live. There will be no new content or updates added to this site. For the latest information, please visit our new site north-standard.com.
A Master's Guide to Hatch cover maintenance webinar written Q&A
News & Insights 29 July 2021
During our recent Q&A webinar on our publication 'A Master's Guide to Hatch cover maintenance', we received many questions from those who registered and joined the live session. Due to time constraints, not all were answered live, however our industry expert panelists have kindly provided written answers to all questions submitted.
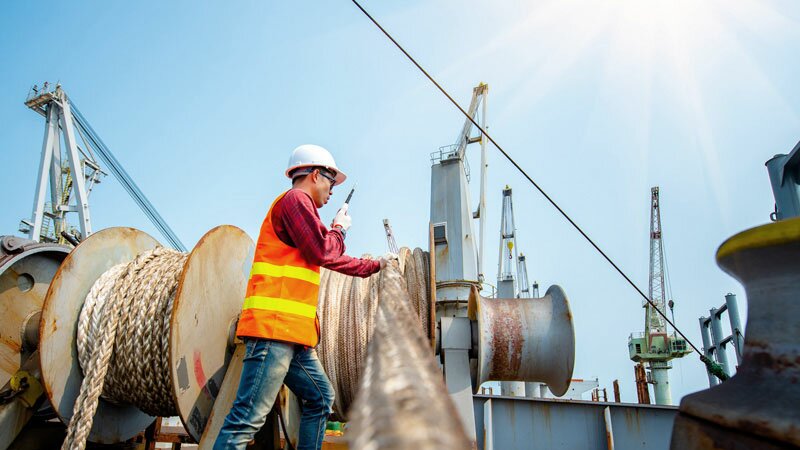
Q&A
1. Are ultrasonic tests compulsory on a regular basis for the hatch covers?
There is no regulatory requirement to conduct ultrasonic leak detect tests of hatch covers on a regular basis. However, it is known that some charterers insist on this, especially if the vessel is engaged in carriage of water sensitive cargoes.
From the club’s perspective, it is strongly advised that ultrasonic tests are conducted at routine intervals to demonstrate the vessel’s cargo-worthiness. Regular testing and maintenance of hatches is more effective and less expensive than wet damage claims.
2. In terms of record keeping and as part of due diligence, would having a clear ultrasonic test suffice? What kind of records would we have to demonstrate that a thorough physical inspection was done?
If a claim for cargo wet damage is filed against the ship, well-documented records are of great value in defending the owner’s interest and proving that due diligence was exercised.
Hatch covers and their fittings should be inspected at the end of every voyage cycle (as per IMO resolution MSC.169(79) and checklists provided in the appendices of the Master’s Guide to Hatch Cover Maintenance) and all findings should be recorded.
Apart from leak detection test records, maintenance-related documents, work orders, spare part orders, work schedules, hatch manual and drawings, onboard checklists, and inspection reports, etc. are recommended to be kept properly filed.
3. If a C/P mentions 'hatches to be watertight', should we presume the logical meaning to be weathertight?
There is a common misconception and a degree of confusion throughout the industry as to whether hatches are constructed to be watertight or weathertight. A watertight closure is designed to withstand water pressure from both sides of the structure, while weathertight means that regardless of the sea conditions, water will not penetrate the ship.
As per the International Convention on Load Lines, hatch covers are constructed to be weathertight. As such, if the C/P contains the statement requiring ‘hatches to be watertight’ then this should be clarified and corrected accordingly.
4. Please give an example of a serious accident caused by mis-operation or lack of maintenance of hatch cover.
Lack of maintenance or improper operation of hatch covers could lead to wide-ranging issues like cargo wet damage, personal injury, pollution, etc.
The Master’s Guide to Hatch Cover Maintenance lists several consequences of not maintaining hatch covers correctly. For example, lack of maintenance of hatch cover hydraulic systems and components could result in pollution as well as present a slip and fall hazard.
5. What are the panellists’ views on the use of Ramnek tape to help sealing arrangements? This is usually frowned upon, but several charterers insist that operators do so. What can an operator do in such a situation?
The use of sealing tape or foam fillers could be considered as an extra precaution, but these are just temporary measures and not a substitute for having a well-maintained hatch cover.
There is a section in the Master’s Guide on this, where it is mentioned that using sealing tape or foam fillers may give a false sense of security as these can be easily washed away by waves.
Furthermore, its usage may indicate that the ship is aware of the potential leakage of the hatch covers. If the cargo receivers are presented with such an evidence, shipowners would be in a weak position in cargo claim negotiations.
6. The drain pipes on our ships are provided with a rubber hose. There are no fire caps or screw plugs. Can you please clarify if this is acceptable?
Drain pipes should ideally be fitted with non-return v/v so that water does not enter the hold. Rubber hoses may not be very efficient in ensuring this. Though we are aware that IACS rules accept tapered hoses as an equivalent effective means for preventing ingress of water from outside. However, these hoses are not effective in maintaining the gas-tight integrity of the cargo holds, if needed.
The drain pipes fitted with screw plugs (or fire caps), assist in maintaining the gas-tight integrity of the cargo holds, i.e., in case of fumigation of the cargo holds, or in case of a fire - they prevent outside air from entering in and ensure that the gas (CO2, in case of fire) does not escape out from the cargo holds.
7. Usually, we secure the hatch cover non-return valves when the cargo is fumigated. However, there is a risk of accumulation of water in the double drainage channel which may seep inside the hold and damage cargo. In such cases, what are the recommended best practices?
The risk of water seeping will be minimal if the hatch covers are maintained in a good weathertight condition, and this is verified by way of an ultrasonic test prior to the loading of cargo.
When the cargo is fumigated, fire caps should be closed to seal off the cargo spaces. However, in the event that some seawater penetrates the gasket during heavy weather, it is important that the water does not enter the cargo hold. Hence, it is recommended to open these caps regularly during the voyage (weather permitting) to drain any water. The crew should be mindful of the fumigant gases and use appropriate precautions and PPE to prevent exposure.
8. With single lip seals, what does the expression "compression 15+6" mean?
These are normally rubber flaps which have no compression (used in partly weathertight hatch covers) and which usually come in pairs, hence we speak of a double lip system. So, the type/system should be clarified.
For a normal packing rubber like sponge, flex or sliding seal, manufacturers will usually express a compression range with a minus and a plus value such as 12mm +8/-8, indicating that we have a compression range from 4-20mm.
9. The purpose of hatch cover cleats is to prevent hatch covers from moving while at sea and they do not improve weathertightness while in port. However, when conducting leak test, some surveyors request that cleats be fully tightened, or even overtightened, to achieve accurate results. Can you please clarify if this is necessary?
It is important to emphasize that cleats do not prevent hatch covers from moving. As there will be relative movement between the panels as well as between the panels and coaming, it is important that we allow some (controlled) movement of the panels. Therefore, cleats are fitted with rubber washers as it makes them a bit more flexible.
When the panels are closed and resting on the bearing pads (which they should do when panels are well maintained) then the packing rubber will be compressed up to its design compression and as such a proper seal will be achieved. Remember that the design compression of the rubber is mainly achieved by the weight of the panel and not by tightening the quick acting cleats.
However, when a leak test indicates leaky spots, and with panels resting on the bearing pads, further tightening of the cleats will not result in a tighter seal and better test results (tightening the cleats will not “squeeze” the steel bearing pads, and no extra compression will be achieved).
As such, extra tightening will only make the system too rigid and prevent the panels from moving resulting in extra forces acting on the panels and securing devices when the ship is at sea and parts such as the coaming, crutches, snugs etc will be exposed to high loads and become deformed or even fail. If this happens, the panels will not be properly secured anymore which is an infringement against the Loadline Convention and will put ship, crew, and cargo at risk.
The main goal of making a test should be to ensure that hatch covers will perform well whilst the ship is at sea. This can only be done by evaluating results of a test and visual inspection of the hatch covers. Unfortunately, emphasis is too often placed on passing the test (by all means) so that loading can commence without delay.
Under no circumstances, cleats should be overtightened!
10. Please advise if Vaseline [or another alternative] can be used for the rubber packing?
It is a false belief to think that applying Vaseline (or any other type of grease other than the approved manufacturers grease) will keep the packing rubber in good shape and flexible. Applying Vaseline (which is petroleum jelly) will affect and damage (dissolve) the rubber sealing surface of the packing rubber. Also, the sticky Vaseline will allow cargo remnants and debris (dust, dirt, rust, etc.) to become embedded in the grease which will enhance abrasion and deterioration of the packing rubber. Only manufacturer’s recognised or recommended grease can be used and even then, only apply a fine film and in places where necessary. This will generally be mentioned in the maker’s manual. Some people think that applying loads of Vaseline or grease on the packing rubber (under the pretext that this is good practice) will help in passing an ultrasonic test. By doing so, the strength of a signal may be slightly weakened, but the important leaks will still be detected. Moreover, the grease will be quickly washed away in heavy weather, so the test might have been ‘OK’, but hatch covers will still leak and endanger the ship and crew as well as cargo and will make it very difficult to defend the member’s position.
11. I was interested about your 9 key component parts. Do you have good self-check list by onboard crew members for investigating HATCH COVER KEY PARTS?
Every sealing system and ship is different, and different component parts, clearances and tolerances will be involved. However, the 9 key parts are the most important items that should certainly not be overlooked during an inspection. Best practice is to approach specialists/consultants who can prepare a tailor-made inspection guide and include some additional guidance for the crew to ensure they get things right from the first time.
12. A common area where hatch covers can leak is at the cross joints due to lack of compression. Can you elaborate on hatch covers with Fx stoppers (longitudinal locators)? Do all hatch covers have them? What are the issues faced and how to rectify them?
Panels always have to be guided into the correct sealing position which means that both geometry as well as compression should be correct. However, ships and panels are different and so is the design of locators. You should familiarise with the design of the locators and the maker’s information prior inspecting. The most frequently seen type of defect on locators is wear. It is normal that wear affects the locators during the in-service life of the ship, but generally the importance of respecting the maximum tolerances is not recognised. Acceptable wear is usually not more than 2-3mm (as it relates directly to the design compression of the packing rubber which is also a matter of mm) and if excess wear is not spotted in time by the crew, compression and tightness will suffer with water ingress and claims as a result.
13. What is the usual wear ratio per year for steel-to-steel bearing pads?
Bearing pads will wear down at a rate of 1mm per year, although this is merely a rule of thumb and depends on factors such as type of pads/mating surfaces, trading area, cargoes carried, maintenance etc.
14. Can we use any type of steel to adjust the height of the bearing pads?
No. For steel-to-steel bearing pads, the moving part of the system is made of a harder type of steel than the fixed part. Attention should be paid to the fact that panels should be able to move freely and are not hindered in their movement by wear patterns on the bearing pad system. If pads are hampered in their free movement, then cracks will develop in the pads, panel, or coaming.
15. Should “normal” indents as a result from impact with the stevedore’s loading gear and/or cargo be reported and repaired?
Yes. Officers should be vigilant when compression bars are hit by the stevedore’s loading/discharge gear or cargo. With design compression of packing rubbers being a matter of mm (usually in range of 8-12mm) even a small indent or set down will significantly affect sealing capacity and cause the rubber-compression bar interface to open up under “normal” conditions instead of “extreme” conditions, allowing water entry.
In case of stevedore damage, always pay attention to the fact that repairs are carried out in line with manual specs and by qualified people. Also inform class about the damage as impact damage may not only be limited to visible damage to the compression bar, but also cause damage to the coaming table, coaming stays and/or supporting structure (inside ballast tanks). Always issue a protest letter to hold stevedores responsible in writing as what may appear to be a small damage initially, may end up with a more significant repair (and cost) afterwards.
16. Are packing rubbers designed to compensate for all relative movements between the panels and panels and coaming?
No. Packing rubbers are designed to compensate for a specific range of relative movements. To ensure that the rubber packing will live up to expectations when the ship is in service, the manufacturer’s specs should be carefully observed when ordering new rubber. It is always recommended to buy original spare parts but in case non-original rubber is ordered, extra care should be paid to ensuring that all parameters of the packing rubber are matching. The compensating capacity of a packing rubber will reduce accordingly as wear starts to set in (permanent set). Before repairing rubber, always check if the other component parts are in good condition. If not, adjust/repair those first.
17. What is causing the relative movements between panels?
The ship’s hull is more flexible than the hatch cover panels, so the panels and ship will not move in unison, hence there will be relative movements between the panels and the coaming as well as between adjacent panels.
Also, weather conditions, ship’s draft/loading conditions (hogging/sagging) and hydrostatic pressure on the hull, ice, etc. will influence the hatch/coaming geometry and relative movements.
18. What information relating to hatch covers can we find in SOLAS?
It is not always clear or transparent, but in the various chapters in SOLAS, information is mentioned that may refer to hatch covers and hatch cover tightness. You will find information on issues such as maintenance and repairs/modifications, duty to inform class/flag State, fire protection, fire detection and exemptions, the use of pesticides in ships (fumigation), carriage of dangerous goods (dangerous when wet), management for the safe operation of ships (ISM), additional safety measures for bulk carriers.
19. What hatch cover related information should be included in the ship’s SMS?
Hatch covers are heavy and huge mechanically operated pieces of equipment. Procedures related to maintenance, operational safety, preventing wetting damage, avoiding pollution (leakage of hydraulic oil), damage to property as well as the availability of necessary manuals, drawings and checklists should be considered. Also, the need to have sufficient spares on board should be identified.
20. What type of training can be given to crew about hatch covers?
Training that is related to safety, correct operation, familiarization with emergency procedures and drills, re-use of hatch cover emergency power pack should be considered.
21. Why are hatch covers not weathertight when no sound is heard during an ultrasonic test and readings are below the 10% OHV fail/pass criterion?
Whilst the absence of sound (or very little sound) is normally an indication for proper sealing and compression of the packing rubber, there are several situations whereby no sound does not mean that hatch cover rubbers and covers are in order and that hatch covers will remain weathertight whilst on passage. Hence the importance of a visual inspection to detect problems with the covers and their sealing system.
Also, care should be taken that sound heard during a test is the result from genuine leak sites and is not the result from false echoes or other parasite noises. This is taught to operators during SDT-IMCS training sessions.
22. Should a vessel be rejected on basis of a few localized spot leaks?
Evaluating if the leakage is important or not is a multifaceted and complicated issue. Only people who have a thorough understanding and practical experience with hatch cover inspections, testing and claims should be asked for advice. Some specific issues to be considered are listed below:
- What is the reason for the spot leaks? Is it an occasional defect (stevedore damage to rubber or compression bar) or a recurrent defect (repeated contact of rubber packing with compression bar during opening and closing due to reduction in wheel diameter or trackway height? In the latter case, a simple rubber repair will not fix the problem and may help in passing the test, but the problem will occur again soon so the risk for ingress remains).
- A few spot leaks will generally not cause major water ingress and if water infiltrates, it can normally be evacuated through the drain system so that the risk for cargo damage is limited.
- However, if the spot leaks are known prior to departure, and if it was decided to sail without carrying out (proper and relatively simple) repairs, then the owners/Master may be blamed for not exercising due diligence.
- Also, the type and sensitivity of the cargo to be carried should be considered. Generally, a few spot leaks will not put the ship or crew in danger, but they might cause a cargo claim.
23. Changing the rubber packing on the hatch covers can be very challenging if carried out by the crew. Can work done by crew be a certified and acceptable job?
Whilst there may not be a specific certification requirement, maintenance should be undertaken by suitably trained persons. The amount of training required will be dependent on the complexity of the item/system being maintained and requirements for specialist input and specialist equipment.
With respect to the replacement of rubber packing, Class Surveyors will confirm by examination and testing that the hatch cover is sealed correctly and is tight. If it is not, then remedial work will be required, if the crew is unable to undertake rubber packing renewal correctly then appropriate assistance may be required e.g., from a ship repair firm or from the hatch cover manufacturer.
24. How critical it is to check the condition of the landing pads? What is the criteria used by classification societies when checking landing pads during the surveys?
Landing pads are critical to the correct sealing of the hatch cover, as they determine the amount of rubber packing compression. The satisfactory condition of the landing pads should be checked on a regular basis by the crew and during periodic surveys by the Surveyors. When making repairs to landing pads, the approved as-built drawings and makers manual should be referred to. The Master’s Guide provides guidance on maintenance of landing pads; in the guide it states if wear is greater than 4mm, repair is essential and that landing pads should always be repaired to the original design height.
25. Is it a requirement to check hatch cover weathertightness during the class surveys (annual/intermediate/renewal)?
Yes. At Special Survey the Surveyor is required to confirm that hatch covers are weathertight, by witnessing a hose test and/or ultrasonic test.
At Annual Survey, where considered necessary by the Surveyor, the effectiveness of sealing arrangements may be proved by hose test (and/or ultrasonic test) or chalk testing supplemented by dimensional measurements of seal compressing components.
26. Apart from physically apparent deterioration, is there any fixed duration within which the rubber gaskets must be renewed?
Regulations (Class or Statutory) do not specify a fixed duration (unlike for lifeboat falls for example). Therefore, supplier’s documentation should be consulted to ascertain service life. However, if it is found that the rubber packing has deteriorated e.g., hardened, permanent set, wear damage, and as a result is no longer able provide a seal, then it should be renewed.
27. The hatch cover designs have not evolved over the last several decades. The existing covers are difficult to maintain. Is any new technology on the horizon?
LR Rules allow for the use of alternative materials, other than steel. Designers have and are looking at lightweight composite materials for the construction of hatch covers, reducing weight and eliminating corrosion on the cover itself, but composites present challenges for repair when damaged.
28. Right or wrong: Any hatch cover will leak when water is sprayed long and hard enough on the same spot
A new hatch cover, or a properly maintained hatch cover, should not leak in this situation. As stressed in the webinar and in the Master’s Guide, regular maintenance is required, with attention being paid to the condition of all components because they all contribute to the effectiveness of the seal.
29. Older ships often have issues with misaligned hatch cover panels. How best to repair so they can carry sensitive cargoes again?
The reasons for the misalignment should be investigated and understood, e.g., worn landing pads, stoppers, hinge pins, locators. The Master’s Guide gives guidance on the items to look at. Repairs should then be carried out, with reference to the approved as-build plans and the maker’s manual. If necessary, the advice / input of the maker or specialist company should be sought. It may be necessary to unship the covers and take them ashore or to take the ship to a repair yard, to undertake satisfactory repairs. For sensitive cargoes, where even minor ingress of water is an issue, careful attention needs to be paid to the condition of all components, to try and eliminate all sources of water ingress.
30. When undertaking major repairs to hatch covers and coamings what should be considered?
When undertaking major repairs, the following are key items to consider:
- Repairs are to reinstate the structural components to be as per the approved plans.
- Manufactures’ / makers’ specifications should be followed.
- The Class Surveyor is to be involved and they are to agree the repairs, in order to maintain the validity of the ship’s Class and Statutory Certification.
- Any modifications to the design are to be approved by the Class Society.
- Structural materials of the correct grade are to be used and they are to be certified as per the requirements of the Class Society.
- Repairs to hatch covers may be required to be carried out ashore.
- Welding is to be carried out by qualified welders, working to approved procedures, acceptable to the attending Surveyor.
- Makers / manufactures specified spares / replacement part should be used, where possible.
- NDE is to be undertaken as required by the attending Surveyor and carried out by qualified technicians.
- Final examination and testing of the hatch covers is to be undertaken to confirm satisfactory operation and sealing and is to the satisfaction of the attending Surveyor.
31. How much corrosion / wastage is acceptable on a hatch cover?
On older ships corrosion on hatch covers is assessed as a percentage of the design thickness. So, for example on a General Cargo Ship, a 25% diminution to the hatch cover plating may be permitted by the Class Society.
On newer ships, and on CSR (Common Structural Rules) Bulk Carriers, hatch covers are often designed using a ‘nett scantling’ approach, with a corrosion addition being added to each structural element e.g., 2mm for the cover top plate, 1mm for stiffening structure. This corrosion addition should be shown on the approved plans, if not then the maker/manufacturer and the Class Society should be consulted.
The Class Society should always be consulted with any questions regarding permitted wastage.
The recording of this webinar is hosted on our YouTube channel.
With thanks to:
- Capt. Walter Vervloesem, Chairman, IMCS Group
- Richard Beckett, Global head of Technology – Survey and Inspection, Lloyd’s Register
**We extend our thanks to the Nautical Institute for their image contribution during the webinar presentation and as uploaded with this document.
类别: Loss Prevention